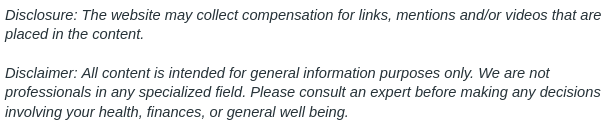
Understanding the importance of safety protocols in manufacturing environments can help mitigate risks of accidents and adhere to legal standards. This article provides a comprehensive guide to effective strategies for accident prevention and minimizing legal repercussions. By focusing on the critical aspects of safety, compliance, and risk management, manufacturers can create a secure and productive workplace and learn how to prevent accidents.
What are the common causes of accidents in manufacturing settings?
Manufacturing settings often come with inherent risks due to the nature of the work involved. Common causes of accidents include machinery malfunction, inadequate training, and poor maintenance practices. Addressing these factors is crucial for any factory aiming to improve its safety records and avoid the need for a personal injury lawyer.
Human error is another significant contributor to workplace accidents in manufacturing. This can be due to distractions, fatigue, or lack of familiarity with equipment, such as CNC router machines. Implementing comprehensive training and supervision protocols can help reduce these incidences and ensure the safety of all personnel involved.
Lack of enforcement of safety protocols and failure to conduct regular inspections also lead to accidents. Simple preventive measures, such as regular leak detection and maintenance of equipment, can substantially minimize the risk of accidents. These steps also help in adhering to safety standards and potentially reduce insurance premiums.
How can safety training programs reduce accidents?
Effective safety training programs are essential components in minimizing workplace accidents. These programs should focus on familiarizing employees with equipment, safety procedures, and emergency response actions, which can be financed with a start-up loan for comprehensive training modules. Regular refresher courses ensure the consistent application of safety measures.
The training should not be a one-time event but rather an ongoing process integrated into the company culture. Emergency services for mechanical contracting companies often provide insights and resources for specialized safety training. By building competency through regular drills and workshops, workers can develop the habit of adhering to safety protocols instinctively. This is crucial to learn how to prevent accidents.
Moreover, these programs are beneficial in reducing the number of incidents that could lead to the involvement of a personal injury lawyer. With documented training and procedures, companies can demonstrate their commitment to safety, which is vital if any legal challenges arise. The role of safety training cannot be overstated, as it directly contributes to reducing workplace injuries.
What role does hiring a safety officer play?
Hiring a safety officer at a manufacturing company significantly reduces the risk of accidents and ensures a safer work environment. A safety officer understands how to prevent accidents and is dedicated to identifying potential hazards, enforcing safety protocols, and fostering a culture of caution and accountability among employees. In manufacturing, where heavy machinery, hazardous materials, and high-stress environments are common, the presence of a safety officer becomes essential.
Safety officers conduct regular inspections, risk assessments, and audits to uncover unsafe practices before they lead to incidents. They establish clear procedures for equipment handling, emergency response, and personal protective equipment (PPE) use, reducing the likelihood of workplace injuries. Through targeted training sessions, they educate employees on safety standards, empowering workers to recognize and avoid risky situations themselves.
Moreover, safety officers help the company remain compliant with industry regulations, avoiding potential fines or shutdowns due to safety violations. They maintain up-to-date records, ensuring transparency and readiness in the event of an inspection. By mitigating the risk of accidents, safety officers protect the well-being of employees and the financial health of the company, reducing costs associated with worker’s compensation, liability, and equipment damage, ultimately fostering a more productive and secure workplace.
What role does safety equipment play in accident prevention?
Safety equipment is a cornerstone of understanding how to prevent accidents in the manufacturing sector. This includes personal protective equipment (PPE) as well as machinery safety features like explosion-proof seals and intrinsically safe barriers. These devices provide essential protection against common workplace hazards.
By utilizing state-of-the-art equipment, manufacturers can greatly reduce the likelihood of accidents. Explosion-proof seals, for example, prevent hazardous materials from igniting or causing explosions. Similarly, intrinsically safe barriers help guard against electrical hazards, which are common in environments with flammable materials.
Overall, the integration of appropriate safety equipment aligns with regulatory standards and helps avoid potential legal ramifications. When selecting equipment, companies should work closely with suppliers to ensure they meet both safety and operational requirements. Properly implemented safety measures contribute significantly to a safer workplace environment.
How can manufacturers ensure compliance with legal regulations?
Compliance with legal regulations is essential for manufacturing operations. Understanding and following regulatory requirements not only improve safety but also protect companies from legal repercussions. Manufacturers need a robust compliance strategy that includes regular audits and the use of up-to-date technology like intrinsically safe barriers.
Working with regulatory bodies to stay informed about changes in safety standards is also crucial. This includes maintaining open communication channels with these organizations and retaining documentation as evidence of compliance. A proactive approach ensures that companies consistently meet or exceed legal obligations.
Regular inspections and the use of services such as crane inspection service play a vital role in maintaining compliance as you learn how to prevent accidents. By conducting frequent assessments, manufacturers can promptly address any potential non-compliance issues. This could be instrumental in minimizing the risk of costly fines and operational interruptions.
What are the best practices for risk assessment in manufacturing?
Risk assessments are a fundamental part of accident prevention strategies. Implementing best practices like systematic inspections and leak detection can help identify potential hazards before they result in accidents. Initial and recurrent evaluations also ensure that risk management activities are current and effective.
A comprehensive risk assessment should involve all relevant stakeholders, including employees, safety officers, and management. Involving diverse perspectives can uncover hidden risks and enhance the development of mitigation strategies. The collaborative approach ensures comprehensive protection measures are instituted across the board.
Regular updates to risk assessment strategies are important, especially as equipment or processes change. Utilizing modern technology tools like crane inspection service to monitor and update risk profiles can lead to more informed decision-making. This ongoing diligence in risk management protects both workers and manufacturing assets as you learn how to prevent accidents.
How can fostering a safety culture prevent accidents?
Creating a safety culture within an organization is crucial for accident prevention. Encouraging employee engagement in safety practices helps to instill a sense of responsibility and accountability. This involvement can be facilitated through open communication channels and supported by emergency services for mechanical contracting.
In a robust safety culture, safety practices become ingrained in everyday operations rather than merely procedural requirements. Regular safety meetings, employee feedback sessions, and recognition of proactive safety behavior all contribute to cultural transformation. These efforts lead to a collective effort that minimizes unsafe conditions and practices.
Leadership plays a vital role in cultivating this culture by demonstrating a commitment to safety through actions and policies. By setting examples and enforcing safety protocols, leaders can guide the organization toward sustainable safety improvements. In turn, a strong safety culture can reduce the likelihood of facing a personal injury lawyer by not learning how to prevent accidents.
What is the impact of technology on accident prevention?
Technological advances have significantly enhanced accident prevention capabilities in manufacturing. The adoption of automated systems, like CNC router machines and crane inspection service technologies, can minimize human error and improve operational precision. These innovations can also detect potential hazards earlier, allowing for timely intervention.
IoT and digital monitoring solutions provide real-time insights, enhancing the ability to predict and prevent unsafe conditions. Automated alarms and safety interlocks work together to ensure fast responses during critical events. This proactive use of technology significantly reduces the risk of accidents occurring within manufacturing settings.
Investing in technology can offer a competitive edge by elevating safety measures, compliance, and operational efficiency. While implementation costs may be significant, businesses can explore options like a start-up loan to finance technological upgrades. Overall, the benefits of integrating technology in accident prevention strategies far outweigh the initial investment.
How should emergency response plans be structured?
Strategically planned emergency response protocols are crucial for effective accident management. Detailed emergency plans should outline clear roles, responsibilities, and procedures for all potential scenarios. This includes response measures for specific equipment like CNC router machines, as well as coordinated efforts with emergency services for mechanical contracting.
Comprehensive drills and simulations are necessary to familiarize employees with emergency protocols. Regular practice sessions ensure that every team member knows what to do during an emergency situation, minimizing confusion and delay. The effectiveness of these simulations should be assessed, with feedback used to refine the emergency response strategy.
Coordination with local emergency services is vital to ensure a seamless response. Establishing partnerships with these entities and conducting joint drills can enhance preparedness. A well-structured emergency response plan is an invaluable tool for protecting employees and property, and it significantly reduces potential legal repercussions.
What legal consequences can arise from workplace accidents?
Workplace accidents can lead to significant legal ramifications, including fines, lawsuits, and operational shutdowns. Employers may face litigation from injured employees, often necessitating the involvement of a personal injury lawyer. Settlements and judgments can be costly and damaging to a manufacturer’s reputation.
Regulatory bodies can impose fines or other penalties for non-compliance with safety standards. Consistent failure to meet regulatory requirements can result in further inspections, sanctions, or even restrictions on operations. It is crucial to understand these potential consequences and take proactive steps to mitigate any legal liabilities.
Furthermore, workplace accidents can affect employee morale and lead to higher turnover rates. In some cases, there may be a need for logistical revisions to prevent further accidents, impacting productivity. Manufacturers need to prepare for these possibilities by maintaining rigorous safety protocols and legal readiness strategies like partnering with a knowledgeable personal injury lawyer.
How can taking safety measures in your manufacturing company save money?
Implementing safety measures in a manufacturing company is not just about protecting employees; it’s a strategic investment that can yield significant cost savings. By prioritizing safety, companies can reduce the financial strain caused by workplace accidents, injuries, and production downtime.
Accidents often lead to costly consequences, including medical expenses for seeing a doctor, workers’ compensation claims, and potential legal fees. Additionally, injuries can result in lost productivity as employees recover or require replacements, further impacting overall efficiency. For example, a worker who breaks a bone may require the services of a bone graft delivery device for proper healing. Safety measures such as regular training, routine inspections, and enforced use of personal protective equipment (PPE) help prevent these incidents, ensuring a smoother, uninterrupted workflow.
Moreover, manufacturing companies with robust safety programs can lower insurance premiums and help you learn how to prevent accidents. Insurance providers often view safety-conscious companies as lower risk, potentially offering better rates. Adherence to safety protocols also minimizes the risk of costly fines and penalties from regulatory bodies, such as OSHA, for non-compliance with industry standards.
Safety measures also protect valuable machinery and equipment from damage caused by misuse or accidents, reducing repair and replacement costs. Ultimately, a proactive approach to safety reduces financial risks, boosts employee morale and productivity, and strengthens the company’s reputation, making it a smart financial decision for long-term sustainability.
How can manufacturers prepare for legal challenges related to accidents?
Pre-emptive legal preparation is essential for manufacturers to effectively handle potential legal challenges arising from accidents. Retaining a personal injury lawyer experienced in workplace incidents can provide invaluable legal guidance. These experts can help navigate complex legal landscapes, potentially saving significant costs and resources.
The documentation of safety practices, training programs, and compliance with regulations is crucial as you learn how to prevent accidents. Maintaining thorough records of all safety-related activities serves as a layer of defense during legal evaluations. It demonstrates an organization’s commitment to safety and due diligence in preventing accidents.
Regular reviews and updates to legal strategies ensure they are aligned with current regulations and industry standards. Manufacturers can mitigate the impact of legal challenges by adopting a proactive stance that supports ongoing risk management practices. This approach not only enhances safety but also provides peace of mind for the organization and its employees.
Learn how to prevent accidents and avoid legal repercussions by focusing on ongoing dedication to safety, compliance, and continual improvement. By taking proactive measures, manufacturers can create a safer work environment and minimize potential legal liabilities. A thorough understanding of safety protocols and legal requirements is integral to the sustainable success of any manufacturing enterprise.